Safety Stock Optimization to Improve Inventory Health
- Kyle Jurczak
- Aug 6, 2024
- 3 min read
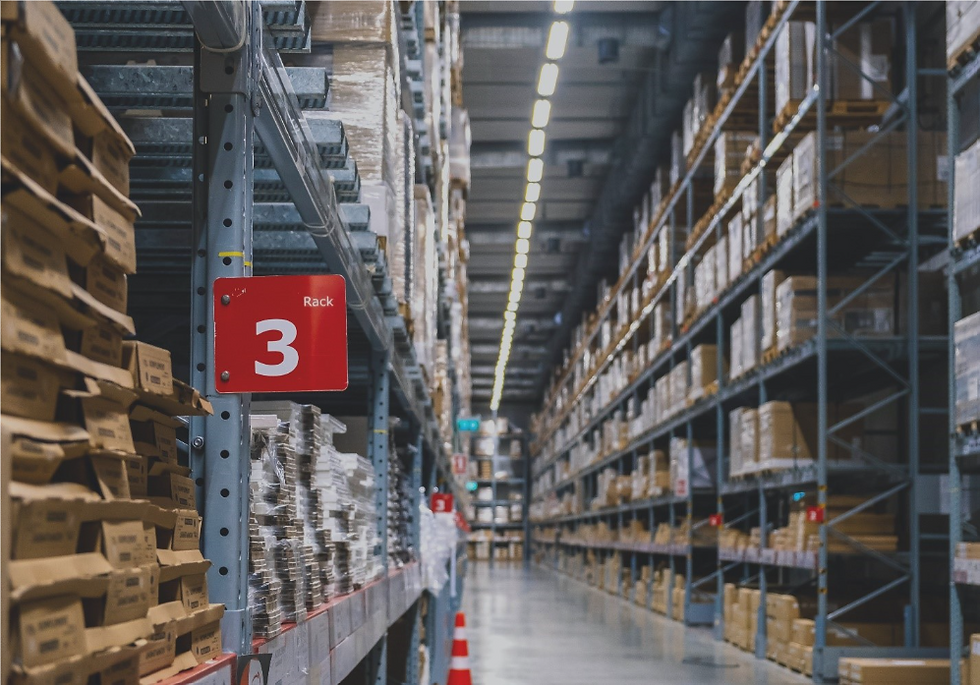
Background:
A leading global CPG company began to have inflated inventory post-COVID due to prolonged supply chain disruptions and unpredictable demand. Up to this point, the method of setting safety stock was spreadsheet-based, lacking the rigor and agility needed for frequent recalculations as the underlying data changed. This led to many interventions by planners due to trust issues with the data. Additionally, setting safety stock levels manually is an imperfect task, requiring the planners to balance many metrics while also being influenced by prior decisions that no longer represented the current inventory state. This resulted in a time-consuming process that was prone to biases and non-optimal safety stock levels. To help solve this problem, the company targeted setting up an inventory optimization process that would dynamically make safety stock recommendations for each item, along with a diagnostic analysis tool both for the model results and the overall inventory health.
Challenges:
Fluid Company Goals & User Inputs: While the project was initiated due to inflated inventory counts, with a constantly changing supply chain landscape, it is possible that the main inventory directives from the company could change over time. This could include the target service level, or even which items are in scope, as examples of what the model had to consider, taking user inputs into each run.
Product Variety: The company has a wide variety of products ranging from popular high-demand items to new products that are just hitting stores. The team had to ensure that the right set of items are considered for the model, and that it would result in appropriate recommendations for differing data inputs
Model Adoption: The inventory planners have an intimate knowledge of the items they set safety stock levels for, making it a challenge to build a model that would produce results that the planners can trust to accompany their own expertise
Results Monitoring: To determine the success of the model, the team needed to determine a method on when to start considering the effectiveness of a new setting, as it takes time for the planning systems to begin planning to the updated setting
Data Sources: The company utilizes multiple data systems, requiring a solution that took data from a variety of sources, while also presenting the output in an appropriate manner to easily implement the safety stock recommendations back into the systems
Solution:
The core of the solution was a multi-echelon inventory optimization model that incorporated data from multiple sources, user inputs, and specific inventory metrics such as demand and forecast history, manufacturing frequency, and product lead times to produce a final safety stock recommendation for each relevant product.
Using the front-end user interface, the inputs could be inspected and validated - along with user inputs added - before the inventory lead would start the model run. Once the model run was complete, the results could also be validated before being sent to individual planners for further review. This final review step provided planners with the necessary data to determine whether to accept the model inputs or make modifications to the recommendation given their additional knowledge about the product. Once the safety stock setting process was complete, the results would be entered into the company's planning system. After additional iterations, this interaction with the results would allow the planners to build trust in the model, thus accepting a higher percentage of recommendations over time, leading to a more optimal and efficient process for the company.
To track the success of the updated settings, a methodology was created to determine when an item began to be planned to the new setting. Additionally, a descriptive analytics view with a variety of visuals was developed for the inventory team to track historical inventory and projections, days of supply impacts, service levels, and more. These visuals provided the team with an interactive solution to understand the short and long term outcomes of the safety stock settings, and the inventory health across the company as a whole.
Benefits:
The initial results were extremely favorable
Inventory Reduction: Achieved a 22% reduction in inventory, equivalent to $11 million reduction in working capital, while having no negative impact on service levels.
Adoption: Inventory planners quickly adopted the solution into their routine.
Scalability: With the project's success in the target segment, the solution began scaling to other regions, allowing for more savings across the entirety of the company.
Conclusion:
The inventory optimization model significantly improved the CPG company's inventory management by replacing their manual system with a dynamic, data-driven approach, allowing them to address inflated inventory and inefficient safety stock settings. Now paired with results monitoring and appropriate descriptive tools, the company can see their full inventory picture while being in control of their inventory health.